Table of Contents
ToggleWhat is Stepper Motors?
Stepper motor is known by its important property to convert a train of input pulses i.e., a square wave pulses into a precisely defined increment in the shaft position. Each pulse moves the shaft through a fixed angle. So, the stepper motor is an electromechanical device which actuates a train of step movements of shaft in response to train of input pulses.
The step movement may be angular or linear. There is one-one relationship between an input pulse and step movement of the shaft. Each pulse input actuates one step movement of the shaft.
When a given number of drive pulses are supplied to the motor, the shaft gets turned through a known angle. The angle through which the motor turns or shaft moves for each pulse is known as the step angle, expressed in degrees.
As such angle is dependent on the number of input pulses, the motor is suitable for controlling position by controlling the number of input pulses. Such system, used to control the position is called position control system.
The average motor speed is proportional to the rate at which the input pulse command is delivered. When the rate is low, the motor rotates in steps but for high rate of pulses, due to inertia, it rotates smoothly like DC. motors. Due to this property, it is also used in speed control systems.
These motors are available in sub-fractional horsepower ratings. As the input command is in pulses, the stepper motor is compatible with modern digital equipment.
Due to its compatibility with digital equipment, its market is greatly increased in recent times. The stepper motors are widely used in X-Y plotters, floppy disk drives, machine tools, process control systems, robotics, printers, tap drives and variety of other industrial applications.
Types of Stepper Motors
The stepper motors can be divided into three categories:
- Variable Reluctance Stepper Motors
- Permanent Magnet Stepper Motors
- Hybrid Stepper Motors
Variable Reluctance Stepper Motors
Variable Reluctance (VR) Stepper Motors are a type of stepper motor that utilize variable reluctance principles to achieve precise positioning and control.
Stator ha electrical windings (coils) arranged in phases. Rotor has toothed ferromagnetic material (no permanent magnets). Bearing has supports shaft rotation. Housing is encloses motor components
The motors have a stator which is usually wound for three phases. The stator has six salient poles with concentrated exciting windings around each one of them. The stator construction is laminated and assembled in a single stack.
The number of poles on the stator and rotor are different. This gives the motor ability, 1. of bidirectional rotation 2. self-starting capability.
Variable Reluctance Stepper Motors offer reliable operation, high precision, and cost-effectiveness, making them suitable for various industrial and commercial applications.
Applications: 3D printing, CNC machines, Robotics, Medical devices, Automotive systems, Textile machines, Packaging machinery.
Permanent Magnet Stepper Motor
A Permanent Magnet (PM) Stepper Motor is a type of stepper motor that uses permanent magnets as its rotor. Stator: Electrical windings, Rotor: Permanent magnets.
Principle: Electrical pulses applied to stator windings. Magnetic fields generated, interacting with rotor magnets. Rotor aligns with stator magnetic fields, resulting in step-by-step rotation.
Permanent Magnet Stepper Motors are widely used in precision applications requiring accurate positioning and control.
Applications: 3D printing, CNC machines, Robotics, Medical devices, Automotive systems.
Hybrid Stepper Motor
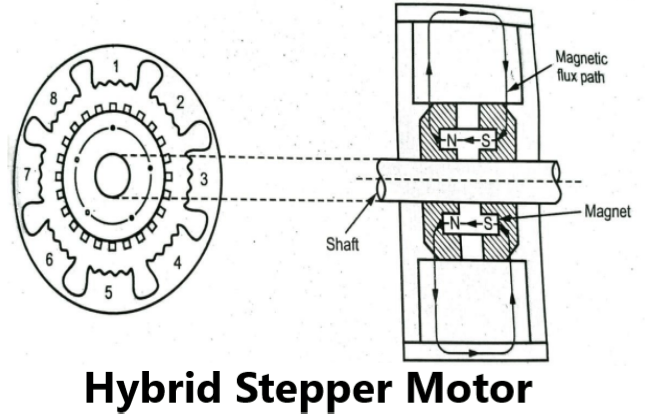
The hybrid stepper motor uses the principles of the permanent magnet and variable reluctance stepper motors. In the hybrid motors, the rotor flux is produced by the permanent magnet and is directed by the rotor teeth to the appropriate parts of the airgap.
The permanent magnet is placed in the middle of the rotor. It is magnetized in the axial direction. Each pole of the magnet is surrounded with soft-toothed laminations.
The main flux path is from the north pole of the magnet, into the end stack, across the airgap through the stator pole, axially along the stator, through the stator pole, across the airgap and back the magnet south pole via another end stack.
There are usually 8 poles on the stator. Each pole has between 2 to 6 teeth. There is two phase winding. The coils on poles 1, 3, 5 and 7 are connected in series to form phase A while the coils on poles 2, 4, 6 and 8 are connected in series to form phase B. The windings A and B are energized alternately.
When phase A carries positive current, stator poles 1 and 5 become south and 3 and 7 become north. The rotor teeth with north and south polarity align with the teeth of stator pole 1 and 5 and 3 and 7 respectively. When phase A is de-energized and phase B is excited, rotor will move by one quarter of tooth pitch.
The torque in a hybrid motor is produced by interaction of the rotor and the stator produced fluxes. The rotor field remains constant as it is produced by the permanent magnet. The motor torque Tm is proportional to the phase current.
Following are the main advantages of the hybrid stepper motor:
- Very small step angles up to 1.8o .
- Higher torque per unit volume which is more than in case of variable reluctance motor.
- Due to permanent magnet, the motor has some detent torque which is absent in variable reluctance motor.
Applications of Stepper Motors
Due to the digital circuit compatibility of the stepper motors, they are widely used in computer peripherals such as serial printers, linear stepper motors to printers, tape drivers, floppy disc drivers, memory access mechanism etc. The stepper motors are also used in serial printers in typewriters or word processor systems, numerical control of machine tools, robotic control systems, number of process control systems, actuators, spacecrafts, watches etc. X-Y recorders and plotters is another field in which stepper motors are preferred.