Table of Contents
ToggleFaraday's First Law
Faraday’s First Law states, during electrolysis process , the amount of chemical reaction take place at electrode under the influence of electrical energy is proportional to the quantity of electricity passed through the electrolyte.
M x Q x I.T
Where “m” is the weight of substance liberated, T is the steady current flowing through the electrolyte and T is time of current flow in seconds.
M x I.T or M= Z.I.T
Where Z is constant and is called Electrochemical Equivalent (E.C.E.) It is expressed in milligram/coulomb.
Faraday’s Second Law
When the same quantity of electricity is passed through different electrolytic the weights of the substances liberated from each will be proportional to their chemical equivalent or equivalent weights.
Chemical Equivalent= Atomic Weight / Valency
Since, atomic weight of hydrogen is unity and so also its valency. Therefore, its chemical equivalent is I.
Process of Electro-Deposition or Electroplating
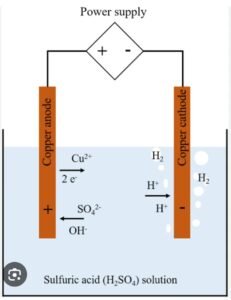
The solution of a salt when used for electrolytic process is called on electrolyte. If two electrodes are dipped into the electrolyte and potential difference is applied across the electrodes the electrode connect to the positive terminal of the supply is known as anode and the other connected to the negative terminal of the supply is called cathode.
In the electrolyte, the molecules of the salt dissociate into two ions. one of which are positively charged called and the other are negatively charged called ions. As we known that opposite charges attract each other, therefore, anions attracted by the Anode and cathode attracted by the Cathode.
For example, when copper sulphate (CuSo4 ) is dissolved in water, immediately molecules of CuSo4 break up into positively charged Copper ions & negatively charged sulphate ions. If two electrodes are dipped in such a solution and a potential difference is applied b/w them as shown in figure.
The positively charged copper ions will move towards the Cathode and the negatively charged Sulphate ions will move towards the anode, it will give out two electrons and become (So4 ) radical. This So4 radical is unstable it reacts with water & produces oxygen which will be given up at the anode and also sulphuric acid which will get dissolved in water. If the anode is a copper plate, H2 So4 will react with it produce copper sulphate, Thus, the copper will be dissolved from the anode to form copper sulphate. The strength of the electrolyte shall remain the same.
When copper sulphate is dissolved in water
(CuSo4 )—–Cu++ +So4–
At anode:- So4 —2e=So4
2H2O+2So42H2So4
When H2 So4 reacts with anode (which is made of copper) H2 So4+Cu=CuSo4+H2
At anode:- Cu+++2e=Cu (This copper gets deposited on the article to be electroplated).
In the Process of Electro-deposition, the operations which are involved in the electroplating process are:-
1.Cleaning of surface
2.Deposition of metal
3.Polishing and buffing
Cleaning of Surface
Electroplating is always done a clean surface. So, the object to be electroplated is thoroughly cleaned. If it is not done, the deposits, formed are not well adherent to the base and is likely to peel off. So, proper attention must be given for cleaning operation.
Deposition of Metal
The process of depositing metal over another metal or non-metal by electrolytic process is known as electro-deposition or deposition of metal. The very common example of this is electroplating. The article to be electroplated is made Cathode in all types of metal deposition processes. The solution or electrolyte is made of the salt of the metal to be deposited and the anode is made of the same metal which can be deposited on the surface of other metals are given below. (1) Copper plating. (2) Gold plating. (3) Silver plating. (4) Nickel plating. (5) Chromium plating.
Polishing and Buffing
Polishing:- Silver, nickel or chromium plating requires polishing. Polishing is done by mops driven at a peripheral speed of 2000 to 3000 meter minute. Mops may be of leather, canvas or fell. It is important to run these mop at high speed.At higher speeds, the metal flows from tops to the valleys of the scratches under high pressure and temperature and produce smooth and shining surface after polishing.
Buffing :- Buffing is a general type of polishing process and is done to make the surface of metal, which is to be electroplated more fine.
I like this post, enjoyed this one thanks for posting. “The basis of optimism is sheer terror.” by Oscar Wilde.
Pingback: What is Electrolysis and Industrial application
Having read this I thought it was very informative. I appreciate you taking the time and effort to put this article together. I once again find myself spending way to much time both reading and commenting. But so what, it was still worth it!
When I originally commented I clicked the -Notify me when new comments are added- checkbox and now each time a comment is added I get four emails with the same comment. Is there any way you can remove me from that service? Thanks!
Hi electricalsphere.com admin, Your posts are always a great source of knowledge.
Thanks for appreciation.
For more electrical Knowledge, Please follow my Insta/Telegram/Whatsapp group.
Now, my focus on spread my website content to more readers.
To boost my moral, Please share my website to your friends.
886141 202823Good read, I just passed this onto a colleague who was performing some research on that. And he in fact bought me lunch as I identified it for him smile So let me rephrase that: Thank you for lunch! 369020
Thanks for appreciation
Please share my web to your friends group
Follow my social group