Table of Contents
ToggleIntroduction
At start the squirrel cage induction motor is just like a transformer with short-circuited secondary and, it will draw heavy current (5 to 7 times the rated full load current) from the supply lines if rated voltage were applied at start.
OF course, the induced emf in the rotor circuit decreases with the increase in speed of motor rotor and consequently both the rotor and stator currents drop to values determined only by mechanical load. It is essential to reduce the starting current to an extent that the line voltage drop does not affect the operation of other equipment connected to the same distribution work.
One obvious way to reduce the starting current is to impress the lower voltage across stator winding at start. The objection to it is that it reduces the starting torque as the starting torque varies as the square of impressed voltage.
The various methods of starting squirrel cage induction motor are given below.
Reduced Voltage or Line Resistance Starter method
In this starting method, reduced voltage across stator windings is obtained by inserting external resistances in each stator lead at start. After a definite time, when the motor picks up the speed, accelerating contacts close and short-circuit the starting resistances and apply full rated voltage to the motor terminals. If voltage across stator terminals is reduced to K times of the line voltage V then at start
Voltage applied to motor = KV
Starting Current, Ist = KIsc
Starting torque, Tst = K2Isc
Though this starting method is simple and cheap but lot of power is wasted in the external series resistors.
Auto-transformer Starting method
In this starting method reduced voltage is obtained by taking tappings at suitable points (50,60 and 80 per cent points) from a 3-phase auto-transformer. Auto-transformer starters may be either manually or magnetically operated. This type of starter is used both for star-connected as well as delta-connected motors. If the transformer tapping used reduces the voltage V to kV then starting line current will be K2Isc and starting torque will be K2 times the torque developed by direct switching.
Star-Delta Switching method
The star-delta starter connects the three stator windings in star across the rated supply voltage at start and after the motor picks up the speed re-connects them in delta across the same supply voltage. It reduces the starting line current and starting torque to one-third of those obtained with direct switching.
Direct on Line Starting method or Full Voltage method
Squirrel cage motors of capacity upto 1.5 kW, double cage rotor motors and squirrel cage motors of large capacity having a high rotor resistance are started by this method. The starting torque with DOL starting is given as
Tst = (Isc/IF) Sf Tf
Where Sf, If and Tf are slip, current and torque respectively at full load and Isc is the short – circuit current.
Starting of slip-ring induction motors
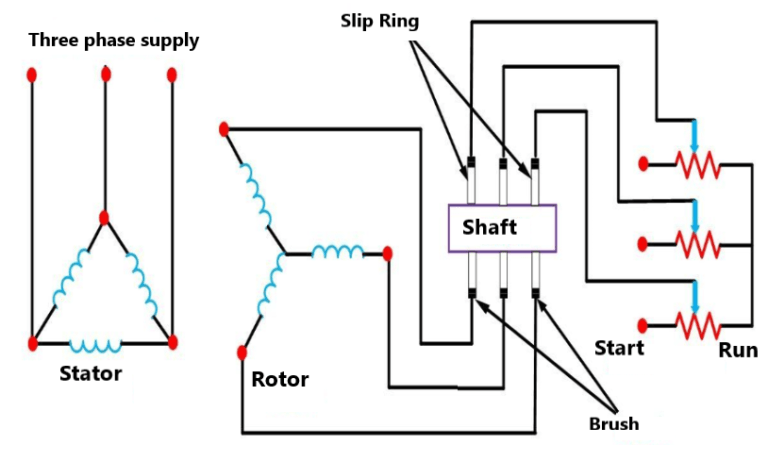
Though the methods described above can be employed for starting 3-phase induction motors of both types namely squirrel cage as well as slip-ring induction motors but are usually employed for starting squirrel cage type motors.
Slip-ring induction motors are usually started with full line voltage across the stator terminals and by introducing variable resistance in each phase of the rotor circuit. Such a starting method, called the rotor resistance starter, cannot be employed in case of squirrel cage induction motors because external resistance cannot be introduced in squirrel cage motor.
The external resistance introduced in each phase of the rotor circuit not only reduces the current at the starting instant but also increases the starting torque due to improvement in power factor. For small and medium size motors face-plate starters are used but for large size motors liquid starters are used.
Pingback: No load and Locked/Blocked Rotor Test on 3-phase Induction Motor - Electricalsphere
Pingback: Interview Question on Electrical Motor
Pingback: Shaded Pole Induction Motor
Its such as you read my mind! You seem to know a lot approximately this, such as you wrote the guide in it or something. I think that you simply can do with some to power the message home a little bit, but instead of that, that is great blog. An excellent read. I will definitely be back.
Awsome info and straight to the point. I am not sure if this is in fact the best place to ask but do you folks have any ideea where to hire some professional writers? Thanks in advance 🙂
We are a gaggle of volunteers and opening a brand new scheme in our community. Your site offered us with useful information to paintings on. You have done a formidable process and our entire group shall be thankful to you.
Adorei este site. Pra saber mais detalhes acesse nosso site e descubra mais. Todas as informações contidas são conteúdos relevantes e exclusivas. Tudo que você precisa saber está ta lá.
hi,
thanks for appreciation. Now, my focus on spread my website content to more readers.
To boost my moral, Please share my website to your friends and subscribe my Insta/Telegram/Whatsapp group.
Pingback: How motor starters operate